How to Control Cost Overruns in Your Construction Project
Manage construction project costs efficiently with planning, team knowledge, vendor assessment, materials control, tech, monitoring, and flexibility.
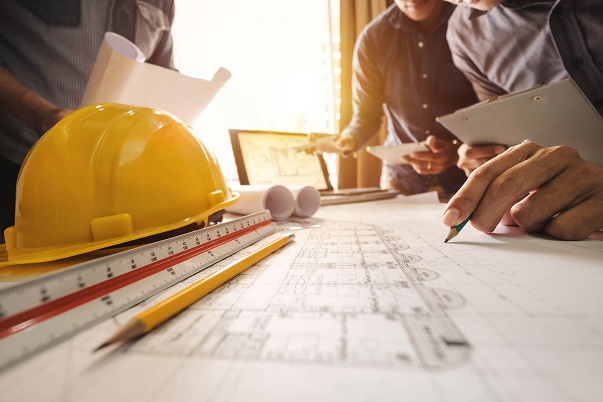
Your construction project can go over budget for many reasons, but it’s usually a combination of the following factors:
- Inaccurate estimates
- Poor design
- Lackluster leadership
- Poor communication
- Worker error
- Poor decision-making
- No motivation
You might notice that all of these factors have something in common: human error and unpredictability. While we often expect perfection from ourselves and others — especially in a high-stakes environment like construction — we’re not the same people from project to project. Our moods and emotions have a more significant impact on our work than we’d like to admit.
So how do we monitor ourselves so that we stay within our budget? Start by delegating more efficiently, relying on the resources available, and understanding where cost overruns originate from.
Types of Cost Overrun
To understand cost overrun, we first have to identify the different types:
- Technical overrun: Underestimating the expenses due to poor data collection.
- Psychological overrun: Underestimating the time and staffing required for a project.
- Political-economic overrun: Misunderstanding of the project’s scope and budget.
When a cost overrun occurs, you spend more time on the project, which can affect payroll, which in turn will negatively affect your reputation. So what proactive measures can you take to nip cost overruns in the bud? Follow these guidelines and you’ll be on your way to controlling costs more efficiently and accurately.
1.Thoroughly Plan Your Project
An estimate is never going to be perfect — that’s what makes it an estimate — but effective planning and the creation of a risk management plan will allow you to prepare for any mishap that might occur during your project.
Planning for the worst doesn’t feel good in the moment, but it puts your mind at ease for the rest of the project and allows you to focus on the task at hand. If something goes wrong, either you have the resources to solve it or you can hand the problem off to someone who does.
Just be honest when you distinguish between “problems I can solve” and “problems I can’t solve.” As we mentioned earlier, poor leadership and decision-making can contribute to more cost overrun and won’t sit well with your colleagues.
2. Know Your Team
Get to know your team members, their strengths and weaknesses, what tools they’re comfortable using, and so on. Knowing what skills your workers have makes it much easier to delegate responsibilities and assign the right people to the right tasks.
Beyond their skills on a construction site, you should also understand their personalities. Perhaps one worker is prone to angry outbursts, and another doesn’t communicate well. When planning your project, take those factors into account so everyone is in the right place.
If you have any new team members that you’re not familiar with, schedule a phone call or in-person chat and talk about your expectations for them on the next project. Gauge their reactions and determine where they fit.
3. Know Your Vendors
Before you agree to a project, you should also get to know the vendor. What is their reputation? If they have a history of poorly managing projects, you should add that factor to your risk management plan.
Determine whether the vendor will accommodate your needs. Make sure their cost estimates align with yours. Outline your risk management plan for them, and ask if you should add any additional information. After all, the vendor should know the grounds better than you.
4. Control Your Materials
While planning your project, you should establish the area where you will store your tools, equipment, and materials. On-site storage is the best and most efficient way, but talk to your vendor and determine the next best spot if it’s not feasible.
You should also constantly communicate about deliveries with your vendor, your employees, and the company supplying the materials. As a result, everyone will be on the same page and you will spend as little time as possible getting everything in place.
5. Control Your Information
Running a construction project requires you to process a lot of information quickly and accurately. From communicating with your vendor to scheduling deliveries to managing employee payroll (among other responsibilities), cost overruns are bound to slip through the cracks — if you process all of the information yourself, that is.
Managing the logistics of your project can be remarkably simple if you use all of the resources at your disposal. Take your construction projects to the next level and incorporate new technologies into your project management.
Technology takes the guessing game out of project planning and thus reduces the chance of cost overrun. Let cloud-based software do the heavy statistical work for you, while you take care of the human aspects of the project, like forming a relationship with your workers and vendors.
6. Closely Monitor Your Progress
In the old days, construction managers monitored their progress by walking the site with pencil and paper. You should still practice that habit to an extent, but you can also use project management tools to monitor your team’s performance.
Suppose the project isn’t going as planned and you need to make adjustments (you should always prepare for that in your risk management plan). In that case, technology will keep everyone up to speed on material deliveries, schedule changes, and payroll updates.
Use the resources available to you, so the whole project stays on schedule and you can focus your labor power on the right tasks.
7. Be Flexible With Your Vendors
Part of managing a construction project is accepting that some factors are out of your control. One of the most common occurrences of cost overrun happens when the vendor orders a halt or delay in construction. If you took this possibility into account while making your risk management plan, you can stay ahead and minimize the damage.
Use technology to shuffle around money and resources, if necessary, so you can focus on putting your workers in the best positions to succeed. When you take some of the logistics off your plate and pass them to reliable software, you suddenly have much more room to deal with the everyday issues that arise during a project.
Set Your Projects Up for Success
Cost overrun is almost always the result of human error and unpredictability. On paper, your project might look smooth and seamless, but it can quickly turn south in practice. You no longer need to rely solely on human resources to run a construction site.
Turn over some of the work to technology and watch things simplify, so you can prepare for any obstacle that comes your way.
Author: Rose Morrison is a freelance writer in the construction industry and the managing editor of Renovated.
- Share This →